Materials Extraction
Work Stream 2
The second phase is extracting active materials from cells, where casing and plastics must be separated for recycling and recovery. The metal current collectors (Al and Cu) are sorted and removed, leaving mixture of active material coating (‘black mass’) or individual particles.
Electrodes extraction involves opening cells, removing and recovering electrolyte and lithium salts for recycling and separating contents – discrete anode assemblies, cathode assemblies and separator. This process enables delamination, where coating is removed using lixiviants and/or ultrasound.
Current technology is mechanical. Beneficiation processes remove fragments of casing and separators. WP2.2 will model and exploit differences in conductivity, density, magnetic, plasticity, size, surface chemistry and wettability to ‘valorise’ black mass i.e. maximise separation (minimising contamination) to enable hydrometallurgical processes to form higher purity, single transition metal carbonate or sulphate products or, with binder removal, enable short loop and direct recycling.
In previous phases, ReLiB made progress and developed IP in ultrasonic delamination, currently being assessed for scale-up with a major international vehicle OEM, which is not ideal for all feedstocks. Further work is required on chemical delamination, which is more suitable for shredded material and offers the potential to delaminate aged electrodes at room temperature without ultrasound.
Debinding removes and recovers the binder used to hold active material together and adhere to the current collector. PVDF is set to remain the preeminent binder in most LIB cathodes and must be removed before refining or direct recycling to prevent fluorine contamination of the cathode oxides.
WP2.1
Electrode Extraction
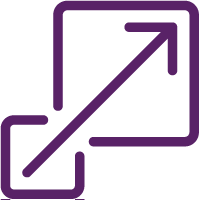
Scope
This package focuses on separation of anode assemblies, cathode assemblies, separators and casing, and recovery of the electrolyte, understanding how disassembly changes with format, chemistry and aging to investigate safe automated methods for cell opening and separating contents into cathode assemblies, anode assemblies and separator. The remit covers electrolyte extraction and drying processes, state-of-the-art measurement and visualization techniques such as Raman spectroscopy, Laue diffraction and image processing to understand and inform the most effective pathway.
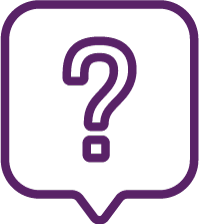
What is Involved
Recycling processes to short loop recycle (regenerate), upcycle or directly recycle electrodes or active materials, uncontaminated anode or cathode materials streams of similar chemistry, morphology and, in some cases, degradation state are significantly advantageous, if not essential.
The ability to separate anodes and cathodes is a critical enabling step for recycling 3.0 and 4.0 processes, such as ultrasonic delamination. Previous phases have shown potential for the automated opening of cell casing and use suction cups to separate contents into three separate piles accurately.
This package will seek to understand and characterise the recovery of electrolyte (lithium salts and organic compounds) through drying (e.g. heating, vacuum) and/or the use of CO2 (liquid and supercritical) employing techniques such as real-time dynamic sampling mass spectrometry, Raman spectroscopy etc. The process seeks to recover the electrolyte in a form to minimise the need for washing of electrodes and enabling electrolyte regeneration and reuse.
In-line characterisation of the active material contained on the electrode assemblies may be needed to identify possible candidate material for direct recycling, or material that requires upcycling to the latest generation chemistry, using rapid visualisation and image analysis techniques to evaluate and categorize the layers within an opened cell and state-of-the-art measurement such as Raman Spectroscopy, Laue Diffraction to enable a rapid and detailed understanding of the composition, morphology and degradation of the active material, necessary for determining how to regenerate or recover the material.
This work will also evaluate emissions or release of powders or vapours and the potential impact on health and safety from any dismantling process.
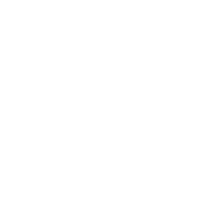
Objectives
- Develop the work in previous phases on automated cell opening and separation
- Explore the impact of cell format on existing opening protocols and develop alternative methods if required (e.g. for cylindrical, prismatic cells, blades)
- Maximise the recovery of lithium salts and organic compounds from electrolyte
- Apply different characterisation / diagnosis techniques to the electrodes that can be evaluated against standard reference points to determine optimal recovery path for active material
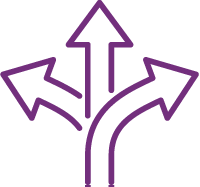
Pathways to Impact
Demonstration on small number cells is achievable in the ReLiB envelope. IUK projects or funding may be needed to enable scale-up to 10s of cells showing the industrial viability of the technology.
WP2.2
Black Mass Valorization
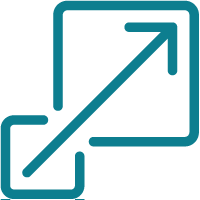
Scope
Characterise and exploit the properties of component materials for improved segregation to produce high purity streams suitable for short-loop and direct recycling from black mass.
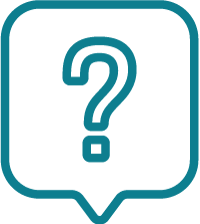
What is Involved
Develop a fundamental understanding of the physical and chemical properties of the sub-components of batteries to exploit (size, density, magnetism, conductivity, surface chemistry & wettability, plasticity, hardness, etc).
Develop separation processes exploiting the properties above. Parameterise and validate physics-based separation models. Predict process yields and models for high efficiency separation and purification (hydromet vs direct recycling).
Using fundamental materials science, exploit differences in the properties of materials to efficiently produce high value, high purity recyclates, tailored for the next recycling step.
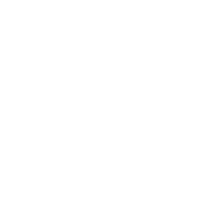
Objectives
- Characterize material bulk and surface, physical and chemical properties of sub-components of LIBs, SSBs, NIBs (future technologies)
- Develop digital twins of separation processes and use physics-based models to predict how material streams will separate
- Exploit properties for separation and produce separated streams of high purity materials suitable for short loop and direct recycling where cell disassembly is not feasible
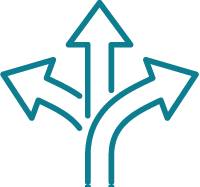
Pathways to Impact
M1–18: Development of materials characterisation library.
M6-24: Model development.
M12–24: Model validation and materials separation.
Previous phases IP is being protected and will be commercialized through the ReLiB TPIP.
WP2.3
Delamination & Debinding
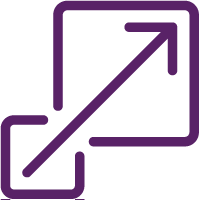
Scope
This package focuses on liberating active material (anode and cathode) from electrode assemblies. Breaking the adhesion between the current collector and active layer can be achieved through delamination. Whilst previous phases of ReLiB successfully developed ultrasonication to achieve delamination, work on chemical (solvent-based) delamination and delamination of shredded material must scontinue. Following delamination, the removal and recovery of binder is required to liberate active material for subsequent recycling or upcycling.
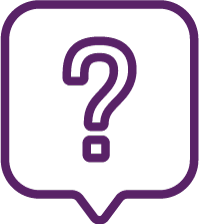
What is Involved
Short-loop recycling and upcycling seek to regenerate, enhance and remanufacture active material in electrodes, owing to high energy and CO2 costs embedded in the fabrication and synthesis of active materials, especially the cathode. To facilitate these refining processes active material must be extracted from the electrode assembly.
The first stage is delaminating the electrode coating from the current collector in an efficient manner. In previous phases we showed ultrasound can successfully delaminate coatings from a variety of electrode assemblies. Preliminary results showed that aqueous solvents and acids are capable of chemically breaking the adhesion between coating and current collector, potentially minimizing contamination caused by introducing metal from the current collector into the waste stream. These processes will be optimised and developed at lab scale and in larger quantities to prove the commercial viability.
Currently PVDF is still used as a binder in most of the EVs being produced. Removal and recovery of the binder plays a critical role in future battery recycling processes and the liberation of active material from end of life batteries. This package seeks to remove all binder from active materials prior to refining. Previous work by CoI Slater has shown PVDF can be a fluorinating agent for metal oxides, substituting fluorine for oxygen within the lattice. Fluorination could severely hamper any upcycling or recycling processes, and this necessitates its efficient removal.
The project also seeks to recover PVDF binder and remove it from the cycle of reuse, as fluorine based polymers will be phased out. This transition will require process(es) to evolve, adapt and develop. This package along with those in WS4 and WS5 will evaluate the design and life cycle of alternative binders and the processes required for removal. The reusability of recovered PVDF – for batteries or other uses – will also be assessed.
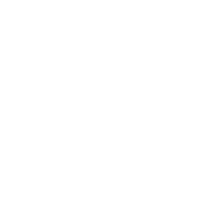
Objectives
- Demonstrate at scale that chemical delamination works for various formats, chemistries, SoH and ages of feedstock
- Demonstrate PVDF debinding on current EoL and production scrap batteries
- Demonstrate and optimise debinding processes for various formats, chemistries, SoH and ages
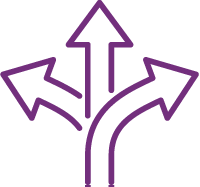
Pathways to Impact
This work builds on processes developed and patented at Leicester and Birmingham providing a platform for the production of high purity black mass/active material streams and will be taken forward through the ReLiB Technology Platform Implementation Plan. Work on PVDF recovery will be in collaboration with a major PVDF manufacturer.